Creating a fully automated print and mail workflow is an important goal to maximize any-sized print and mailing operation. Many of the largest providers already recognize the significant cost savings and quality improvements by leveraging internal Information Technology teams and custom software applications. Thanks to advancements in technology, optimized and automated workflows have become a reality for companies of every size and ability level.
In its most recent “State of the Industry” report, Epicomm shared that over 39% of printers anticipate a more profitable 2016. Where did they anticipate this bottom line improvement coming from? Nearly half of those surveyed cited increased production efficiency. Reducing costs related to labor (26.2%) and rework (16.4%) were also given as ways printers planned to reach the goal.
These are clearly worthwhile goals. However, what tangible steps can a company take to be more efficient, control labor costs, and decrease the amount of costly rework? The answer: evaluate and optimize the systems being used to complete a job to seek places throughout the workflow that can be automated and optimized.
What Is Workflow Optimization?
Simply stated, workflow optimization is a way to boost profitability by reducing the costs, particularly in terms of the time, it takes to accomplish a task. The goal is to get more done in less time, allowing for more capacity and lower per job costs. This can be accomplished through automation and optimized integrations that simplify or reduce the number of steps to accomplish a task. Well-planned and automated workflows can adapt to changing requirements and can reduce the risk for errors that cause delays and rework.
To the mailing industry, this means taking a look at everything from the time a job first appears on the radar during estimation, through preparation, processing, USPS induction, and finally to tracking and reporting. Many mailers employ multiple people using half a dozen or more separate software packages to complete the process shown in the diagram below. Each manually executed step requires time and training, careful coordination of system availability, and increases the risk of costly mistakes.
What Is the Benefit?
The software and hardware used to complete each step in your current workflow is probably sufficient at doing what it was originally implemented to do. However, as customer demands change over time, components were likely added to meet each new requirement. Over time, this leaves a mailing operation that relies on multiple people performing multiple steps to move information in and out of systems. Adding to the confusion, those that are not directly involved in the processing of a job can lose visibility into the status. This makes it nearly impossible to give customers an accurate status update or respond to their question promptly. Perhaps the biggest risk is not knowing if a job is in danger of missing a drop date until it is too late to resolve without impacting other jobs, thus creating a domino effect of lower productivity and dissatisfied customers.
This traditional process is a natural result of evolution within a mailing operation. As needs, customer demands, and USPS regulations change, so does the mix of software and hardware used to meet the requirements. Taking a step back to consider workflow optimization provides an opportunity to see where these systems can be brought together for more efficient completion of every job.
A well-integrated mailing process has many benefits, all of which are aimed at growing your business. By reducing manual steps and handwork, the element of human error is lessened and those resources can be allocated to other tasks. Greater efficiency also controls costs and increases capacity to take on additional work without the need to add resources. An additional benefit of workflow optimization is increased customer satisfaction as quality rises and turnaround times fall.
Where Do I Start?
Take a look at the image included here. Whether you use these exact terms in your operation or not, the overall workflow should look pretty familiar. There are two places you can find opportunities for workflow optimization: within a single process or by connecting discreet processes. In both cases, the easiest opportunity is often found by identifying steps that are repeatable each time. More sophisticated workflow optimization routines look for common tasks and turn elements of a task into variables to make the process repeatable across different environments.
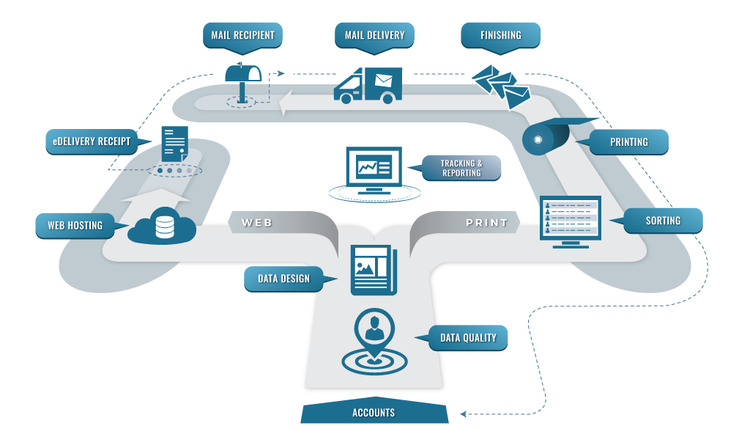
You can start by looking within a single step, indicated by each of the icons in the diagram. Identify the software or hardware you are using to perform each step. Evaluate the sub-steps within each process you complete to see what might be repeatable. Your vendors should be able to help map out each workflow and identify ways to simplify, optimize, or automate.
For example, the presorting step provides ample opportunity to automate processes. Customers often automate each part of their presort process including importing and converting data, address standardization, Move Update compliance (such as NCOALink, ACS, etc.), list presorting, and output of eDocs and production paperwork. These users are able to simply identify a list and kick-off the streamlined process, with each of the individual elements being automatically completed to their predefined requirements.
The next level is to look between steps for opportunities to integrate the handoff from one process into the next. An easy way to get started here: ask your software and hardware vendors if they already have a relationship with one another. You may find that they have already worked together on other projects and have pre-existing integrations you can take advantage of.
Some programs are integrated with multiple print MIS solutions, allowing customers to fully automate their processes from data quality, through printing, finishing, and sorting. Imagine being able to identify a list and job variables up front and have it run through multiple systems without being touched again until the mail has been produced. Seamlessly moving from a list to mail that is ready to be strategically inducted into the USPS delivery network is a great example of an optimized workflow.
Companies across the mailing industry are already reaping the benefits of this type of integration, including reduced time to complete a single job, fewer errors, and greater visibility and predictability into each job. Ask your current vendors what opportunities exist for automation within their environments and what other up and down stream packages they integrate with. You might just find yourself with a healthier bottom line.
Chris Lien is President, BCC Software and a frequent speaker at industry events such as the National Postal Forum. He can be contacted at chrisl@bccsoftware.com